Des usines ultra-connectées chez Renault !
Aujourd’hui, tout est connecté, y compris les machines d’un grand constructeur automobile comme Renault. L’intérêt : collecter toutes les données possibles à chaque étape de la conception, du transport des matières premières à la livraison des véhicules en passant par leur assemblage et la fabrication des différents éléments, pour améliorer la productivité. Explications sur le site de Flins-sur-Seine, dans les Yvelines.
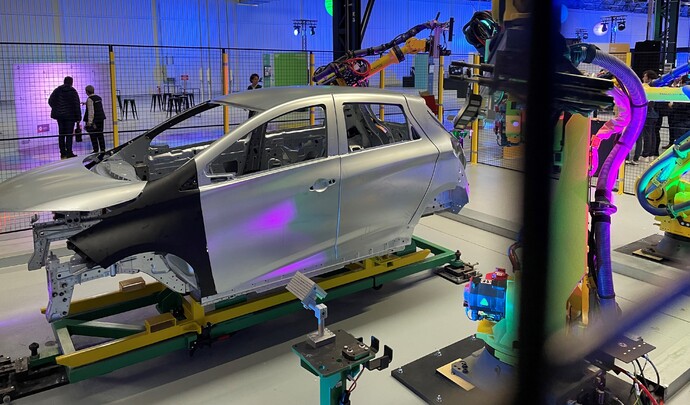
On a beaucoup « brainstormé » sur le site Renault de Flins ce mardi 24 octobre. Les responsables du groupe nous ont exposé leurs projets industriels en nous parlant de metaverse, d’assets, de storage, de compute, de supply chain, de monitor, de backup, de twins, de scope et de digital work station. Du coup, on a beaucoup bossé notre anglais. Et on a compris que le Losange avait franchi un step (pardon : un cap…) en termes de modernité de production.
La première grosse étape a été la mise en place, dès 2019, d’une plate-forme de données regroupant toutes les informations des machines, véhicules et ordinateurs des usines du groupe, et cela à l'échelle mondiale. Riches en enseignements, ces informations permettent d’améliorer au plus vite la maintenance sur les chaînes de montage, la productivité, et de réduire les dépenses en matières premières, énergie, transport, heures de travail, déchets, et émissions de gaz à effet de serre.
En ce qui concerne la maintenance, par exemple : si l'on constate une porosité de pièces de moteurs, pas besoin de tester moult réglages : l’analyse des données passées permet d’isoler le problème rapidement. De même, en cas de pépin mécanique, une alerte ultra-rapide limite voire évite totalement l’endommagement des machines.
Concernant la productivité, l’analyse des consommations de pièces détachées sur plusieurs années permet de réduire le stockage de 30 % et de raccourcir les délais de livraisons. Par ailleurs, le travail sur les chaînes de montage est enregistré par les opérateurs sur tablettes tactiles (4 000 pour 38 usines). Non pas pour l’évaluer, précise la marque, mais pour trouver des axes d’améliorations (formations, équipements, sécurité, requêtes…).
Enfin, les camions de livraison mais aussi les véhicules à distribuer en concessions sont équipés de balises permettant une géolocalisation permanente. Là encore, l’intérêt n’est pas de "fliquer" les livreurs selon Renault, mais d’améliorer et sécuriser l’acheminement.
Quelques chiffres pour imaginer l’ampleur de ce nouvel outil :
-8 500 équipements connectés
-600 équipements dotés de capteurs de vibrations
-60 procédés industriels modélisés (vissage, usinage, soudage, emboutissage, etc.).
-1 milliard de données par jour
Un outil numérique qui évoque immanquablement Big Brother mais qui permettrait de sérieuses économies. D’ici à 2025, Renault espère réduire les coûts de production de 320 millions d’euros, et ceux de stockage de 260 millions d’euros. Par ailleurs, le groupe automobile souhaite réduire ses émissions de C02 de moitié, et les délais de livraisons de 60 %.
Moins de dépenses énergétiques…
Outre ce "data center" révolutionnaire, Renault nous a aussi présenté son programme de réduction des émissions polluantes. Son objectif : une baisse de consommation de 12 % dès 2022, et de 30 % d'ici 2025.
Concernant les dépenses énergétiques de ses usines, la marque travaille bien sûr à couper les machines lorsqu’elles ne servent pas, ce qui, de son propre aveu, n’était pas systématique. D’ailleurs, son système informatique connecté sera d’une aide précieuse pour les agents.
Mais Renault pense également à utiliser des énergies renouvelables, comme la géothermie pour son usine de Douai où est fabriquée la Mégane E-Tech électrique, la biomasse à Maubeuge où l'on assemble le dernier Kangoo, le solaire sur tous les sites bien exposés.
Du côté des pièces composant ses voitures, le groupe étudie de nouveaux traitements pour les disques de freins visant à limiter les émissions de particules fines, l’allègement des pièces métalliques des châssis, berceaux et essieux, une plus large utilisation de plastiques pour les panneaux de carrosserie, la conception locale d'éléments en plastique grâce à des imprimantes 3D, la réduction des tailles des moteurs électriques, l'utilisation des batteries d'un prestataire français (Verkor) pour ses véhicules électrifiés, ou encore la peinture « jet d’encre » pour les teintes bi-ton, qui permet notamment un seul passage par la case vernis et au four… Tout un programme !
Photos (18)
Déposer un commentaire
Alerte de modération
Alerte de modération